Ciment
Inventé par Louis Vicat en 1817, le ciment artificiel est notre savoir-faire historique
Aujourd’hui, notre capacité de production s’élève à plus de 30 millions de tonnes de ciment ! Principal composant du béton, le ciment lui confère un certain nombre de propriétés, notamment sa résistance. Poudre minérale fine, il est obtenu par broyage et cuisson d’un mélange de calcaire et d’argile.
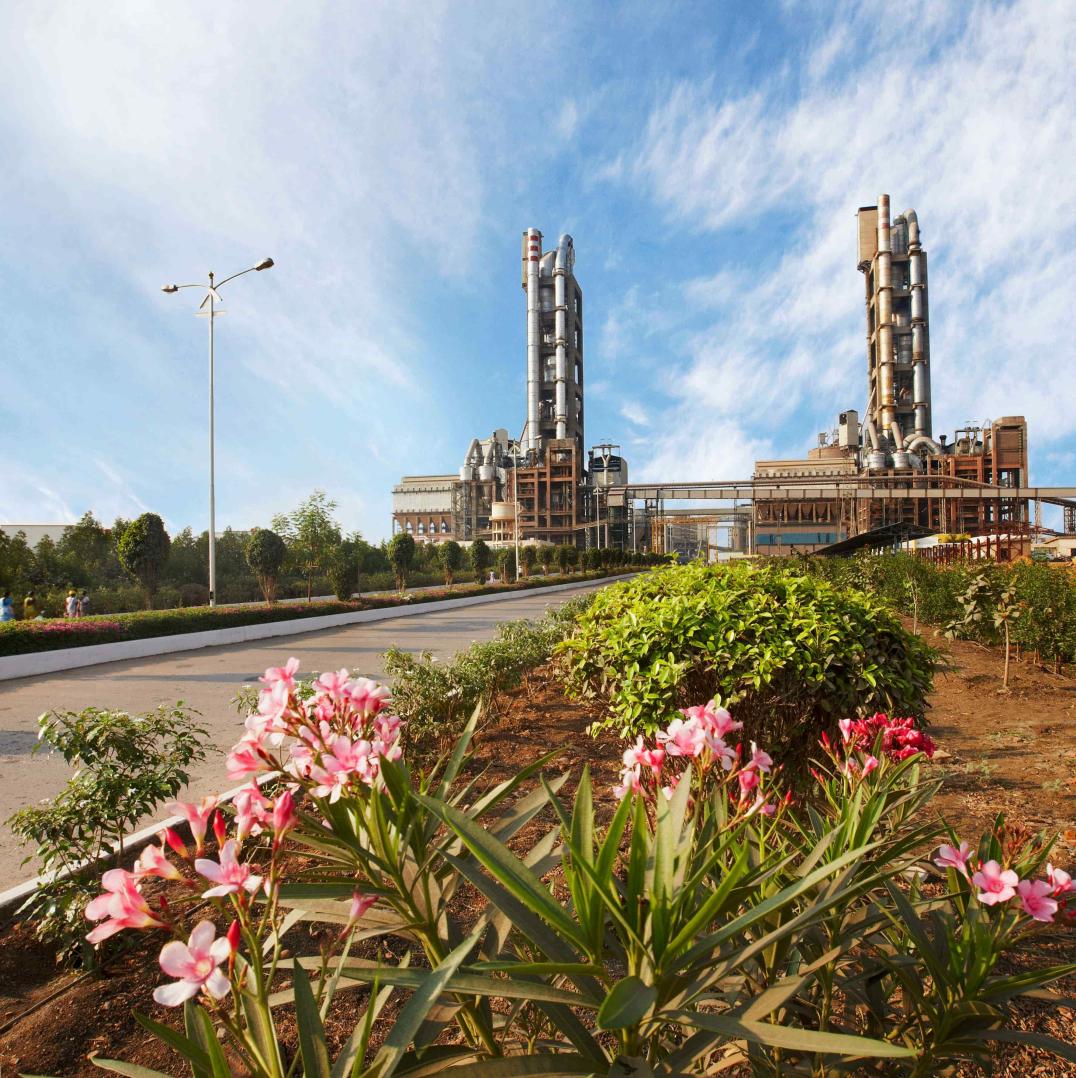
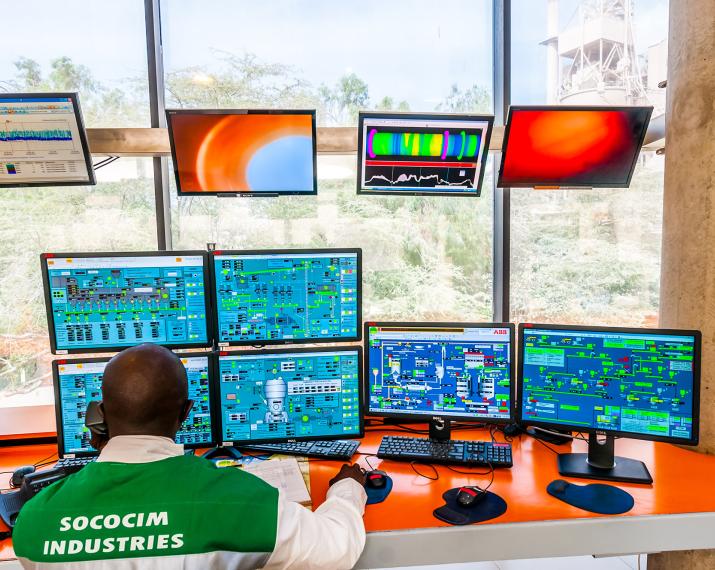
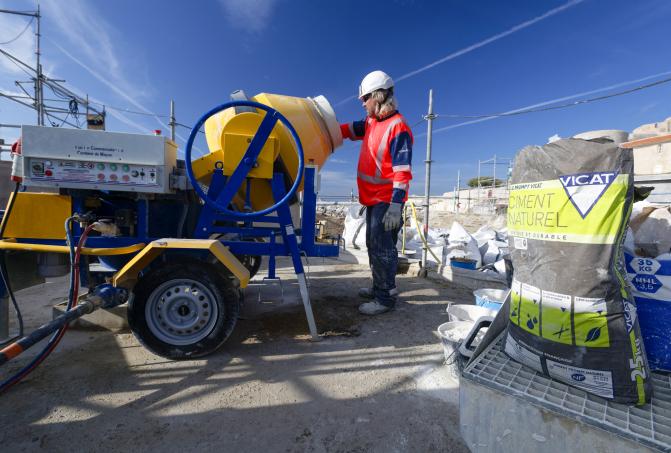
Focus sur
titre
Le Ciment Naturel PROMPT
Issu d'un gisement unique situé dans le massif de la Chartreuse, le ciment naturel PROMPT est une exclusivité du groupe Vicat.
Le ciment PROMPT est un liant hydraulique naturel fabriqué à partir d'une seule matière. Du gisement au produit fini, aucun ajout n'est effectué, d'où son appellation de ciment naturel. Il résulte de la simple cuisson, entre 500°C et 1200°C, d'un calcaire argileux, de composition régulière, extrait de bancs homogènes. La pierre cuite est ensuite concassée puis finement broyée.
Sa minéralogie unique lui confère des propriétés exceptionnelles : prise et durcissement rapides, imperméabilité, faible retrait, faible module d'élasticité, durabilité, prise mer, résistance aux environnements agressifs et aux eaux sulfatées...
L'utilisation du ciment naturel PROMPT est ainsi parfaitement adaptée à de nombreux domaines : maçonnerie rapide, restauration et décoration, éco-construction et eau et assainissement.
Les différents types de ciments proposés
L’expertise de Vicat sur le ciment
Le groupe Vicat produit une large gamme de solutions :
- plusieurs types de ciments artificiel,
- un ciment naturel,
- des liants hydrauliques routiers.
Les différents types de ciments correspondent à des applications spécifiques : la construction résidentielle, la construction d’ouvrages d’art, les travaux souterrains ou encore la réalisation de bétons soumis à des milieux agressifs.
Les différentes propriétés de ces ciments dépendent :
- De la composition chimique des matières premières,
- Des ajouts éventuels de constituants complémentaires lors du broyage (filler calcaire, pouzzolane, cendres, laitiers, de haut fourneau et gypse),
- De la finesse du produit.
Nos principales catégories de ciments sont présentées et classées selon les normes européennes :
CEM I (ciments Portland) et CEM II (ciments Portland composés) : ciments les plus couramment utilisés pour réaliser des ouvrages classiques en béton armé - les ouvrages d’art, les bâtiments industriels et commerciaux et la construction résidentielle. Certains de ces ciments, spécialement formulés, sont également utilisables dans les travaux souterrains en milieux agressifs ou sous la mer.
CEM III (ciments de haut fourneau) et CEM V (ciments au laitier) : ciments usuels à faible dégagement de chaleur durant l’hydratation et à faible teneur en sulfates, utilisés dans les travaux souterrains en milieux agressifs ou dans les travaux à la mer.
CEM IV (ciments pouzzolaniques) : ciments usuels utilisant des produits minéraux d’origine volcanique ayant des propriétés hydrauliques.
Ciment naturel Prompt : ciment spécifique à prise et durcissement rapides, utilisé pour les travaux de maçonnerie rapide, dans l’eau et l’assainissement, mais aussi pour la restauration et la décoration du patrimoine bâti ainsi que dans l’écoconstruction. Ciment historique du groupe (depuis 1970), il est produit à partir d’une pierre alpine naturelle, d’une performance exceptionnelle, offrant une résistance immédiate et élevée ainsi qu’un faible retrait.
De leur côté, les liants hydrauliques routiers ont été développés pour limiter le recours aux matériaux nobles extraits des carrières et pour favoriser les matériaux en place dans les travaux routiers.
Territoires
Nos implantations
- Brésil
- France
- Suisse
- Italie
- Etats-Unis
- Égypte
- Sénégal
- Mauritanie
- Mali
- Turquie
- Kazakhstan
- Inde
6 étapes sont nécessaires à la production de ciment
Les grandes étapes de fabrication du ciment
Etape 1 : l’extraction des matières premières
Les matières premières - le calcaire et l’argile - sont extraits de carrières situées à proximité des cimenteries :
- les rochers et blocs sont abattus à l’explosif,
- ils sont transportés par tombereaux (gros camions) vers des concasseurs pour réduire leur taille à celle de cailloux de moins de 10 cm de diamètre,
- ces matières premières concassées sont triées : leur composition doit comprendre de la chaux, de la silice, de l'alumine et de l’oxyde de fer dans des proportions bien déterminées.
Etape 2 : la préparation du cru
Une fois concassés, les matériaux subissent plusieurs traitements :
- ils sont pré-mélangés dans des halls de pré-homogénéisation pour obtenir une plus grande régularité de composition,
- ils sont séchés et broyés dans un broyeur,
- le broyeur réduit leur taille à quelques dizaines de microns,
- le passage des gaz du four dans le broyeur permet le séchage de la matière et une captation partielle du soufre de ces gaz par la matière broyée.
Appelée farine crue, la poudre obtenue subit de nombreuses analyses chimiques pendant son traitement. L’objectif ? Vérifier que les proportions des diverses matières correspondent à la composition chimique recherchée.
Etape 3 : la cuisson
La cuisson de la préparation est très complexe et se déroule en plusieurs étapes :
- phase de pré calcination : sous forme de poudre, la farine est introduite dans une tour de préchauffage pour être progressivement chauffée par les gaz produits dans le four rotatif jusqu’à 850°C (procédé à voie-sèche). Par gravité, la farine descend dans cette tour.
- production du clinker : la farine est ensuite introduite dans un four rotatif incliné revêtu de briques réfractaires, la température de flamme atteint alors plus de 2 000°C. Cette cuisson entraine plusieurs réactions chimiques complexes :
- le calcaire se décarbonate sous l’action de la chaleur (900°C) et se transforme en chaux
- les argiles se décomposent en silicates et aluminates
- l’ensemble se recombine ensuite à une température d’environ 1 450°C en silicates et aluminates de chaux - le clinker - produit semi-fini aux propriétés de liant hydraulique
- refroidissement du clinker : dans un refroidisseur, le clinker restitue sa température par soufflage d’air à 100°C
Au cours de ce processus complexe, la composition chimique et l’homogénéité de la matière en entrée du four, ainsi que sa régularité dans le temps, sont des éléments fondamentaux.
Le saviez-vous ? Notre four possède des électrofiltres ou filtres à manches qui permettent de filtrer les poussières et donc de limiter les rejets dans l’environnement.
Etape 4 : le broyage du ciment
Le clinker subit ensuite plusieurs traitements :
- il est broyé en grains particulièrement fins (moins de 60 microns),
- la poudre obtenue – ciment - est mélangée à du gypse pour régulariser le temps de prise du ciment,
- d’autres traitements peuvent alors intervenir :
- pour améliorer l'ouvrabilité et la consistance du ciment : ajout de filler de calcaire, de cendres volantes (issues de la combustion du charbon dans les centrales thermiques),
- pour améliorer les propriétés hydrauliques du ciment : ajout de pouzzolanes naturelles ou artificielles.
Etape 5 : le stockage du ciment
Le ciment obtenu est stocké dans des silos de plusieurs milliers de tonnes, parfois divisés en compartiments permettant la conservation de plusieurs qualités de ciment.
Etape 6 : la livraison du ciment
Le ciment est livré en vrac ou en sac :
- En vrac : placés sur un pont bascule, les camions-citernes sont remplis à l’aide de manches télescopiques situées à la base des silos. Le remplissage est contrôlé et les données nécessaires à l’établissement des documents d’expédition et de facturation sont transmises à l’ordinateur central.
- En sac : l’ensachage du ciment s’effectue sur des machines rotatives dont la capacité peut atteindre 5 000 sacs de 35 kg par heure. Les sacs à valve se ferment d’eux-mêmes et un palettiseur les place par lots de 1,5 tonne sur une palette.
Un système de supervision permet de piloter l'ensemble de ces opérations depuis la salle de contrôle, 24 heures sur 24.
Actualités
Retrouvez l'ensemble des actualités